Pipes are unsung heroes as they does many of the important tasks apart from delivering us drinking water. however, the manufacturing process of these pipes are really challenging which impacts industries such as construction, agriculture and energy. Our country has seen growth in different areas be it industrial growth or infrastructure development, which has created high demand for piping system. You can find important role of pipes in different sectors such as sewage systems, oil and gas transportation, water supply or even construction projects. The piping system journey is such a revolutionary tale. Do you want to know about this interesting journey? Then you have landed at the very right page. We are going to discus different stage of pipe manufacturing techniques, pipe manufacturing technologies and some of the future trends that we can predict.
Evolution of Pipe Manufacturing Techniques
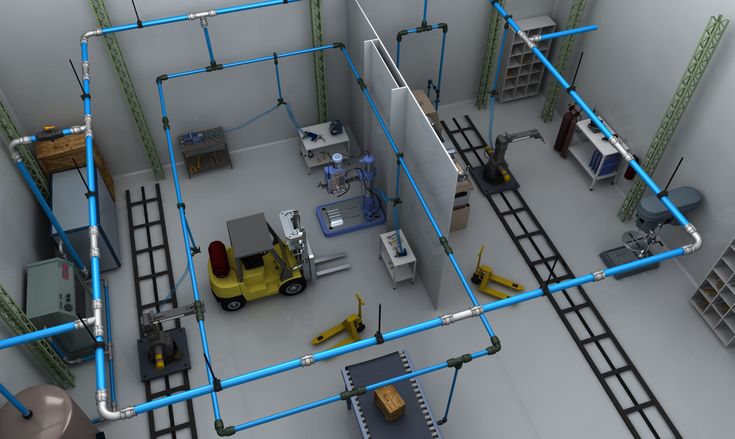
Pipe development stages has been a fascinating journey. There are many of the significant milestones and technological advancements in the path. Let’s have a look at how the process has evolved:
- The early days: natural materials- in ancient times, people used to make pipes by using clay, stone and wood. However, these materials were labour intensive and even offered limited durability. Example: during ancient civilization days, clay pipes were commonly used for water drainage.
- Industrial Revolution: The Metal Era- this era introduced cast iron and steel piping materials. This was a revolutionary step in piping industry. Cast iron pipes started to be used for water and sewage transport. Where steel pipes got famous to offer more strength and versatility. These pipes were commonly used for oil and gas industry.
- The Plastic Revolution: 20th Century- this was time of mid 20th century where PVC (Polyvinyl Chloride) and HDPE (High-Density Polyethylene) was introduced. These pipes offered corrosion resistance, they were lightweight and easy to install and even affordable piping solution as well. Industries started to use extrusion techniques to produce these pipes which made them widely accessible.
- Modern Advancements: Innovation at its Peak- after 20th century industries started to combine composite materials to offer enhanced durability. This started to offer a robust piping solution to different sectors.
So, these were some of the stages of pipe manufacturing techniques. These techniques brought a great revolution to the usage of piping systems
Advancements in Pipe Manufacturing Technologies
The method of manufacturing pipes has become highly advanced over the years. Technology has played a major role for the improvements which led to great help to different industries such as construction, oil and gas and agriculture. There are different manufacturing methods to meet specific requirements, ensure pipes are durable and cost effective. Let’s take a closer look to the advancements in key pipe manufacturing technologies:
- Seamless pipe manufacturing: these pipes are produced without joints or seams. This makes them highly strong and durable. However, the process involves heating a solid piece of metal (billet) then punching a hole through its center. This creates a hollow tube. Further, some of the advanced techniques like rotary piercing and extrusion are used to refine the pipe’s structure. However, these pipes are best for industries that needs high-pressure resistance like oil, gas or power plants. These pipes have joint-free designs which reduces the risk of leaks or failures.
- Welded Pipe Manufacturing: basically welded pipes are made by rolling flat sheets of metal such as aluminum, steel etc. Further, the edges of these metals are welded together to form a pipe. Some of the advanced welding techniques are:
- Electric resistance welding (ERW) is such a fast and cost efficient method. This technology is used for smaller-diameter pipes.
- Submerged Arc welding (SAW) is famous to produce high strength welded pipes for large diameters.
However, welded pipes are commonly used in water pipelines, construction and transportation of non-corrosive liquids.
- Composite pipe manufacturing: composite pipes are made up of different materials. These materials are plastics, fiberglass having metal layers. Combining all of them offers lightweight and flexible pipes. They offer resistance to corrosion and chemicals and they offer high strength as per requirements. Commonly, these pipes are widely used in water distribution, oil and gas and industrial chemical transportation sectors.
- Ductile Iron Pipe Manufacturing: these pipes are improved version of traditional cast iron pipes. These pipes are manufactured by using magnesium to molten iron which gives out a pipe which offers high strength and flexibility. Addition to that, it is resistant to corrosion and pressure. Further, these pipes are commonly used in water supply systems, sewage networks and gas transportation.
- PVC pipes and HDPE pipe manufacturing: when manufacturers started to use plastic like PVC (Polyvinyl Chloride) and HDPE (High-Density Polyethylene), it brought revolution to the piping solution. However, these pipes are manufactured by using extrusion methods. Apart from that these pipes are light weight and easy to install. They offer resistance to rust and chemicals with affordability for large scale projects. Not only this, but these pipes are commonly used in agriculture, drainage systems and building construction.
- 3D Printing in Pipe Manufacturing: this is the next up technology which has emerged as an innovative method for pipe manufacturing. However, this technology saves time and reduces material waste. Apart from that, it also allows rapid prototyping and design flexibility.
Emerging Trends in Pipe Manufacturing
Incorrect pipes manufacturing methods can contribute to delays, quality inconsistency and increased expenses. Not only this, as more people are getting aware of environmental health they are demanding eco-friendly solution. As the demand is high for eco-friendly piping systems it is building up pressure on manufacturers to adopt sustainable practices. Without deploying modern advancements, these problems can take a form of higher operational costs. Important key here would be to incorporate innovative materials, automated technologies and sustainable methods. This can bring a great revolution to pipe manufacturing industries and meet the evolving market of future. Here are some of the most notable trends predicted for upcoming years:
1.Use of Advanced Materials
Manufacturers are preferring to modern materials such as PVC (Polyvinyl Chloride), HDPE (High-Density Polyethylene) and composites. These materials have become industry standard in pipe manufacturing field. however, these materials are durable, lightweight and resistant to corrosion which makes them best for different applications. Not only this, but they are also more sustainable and cost-effective such as iron or concrete.
2.Smart Manufacturing Processes
Automation and precision engineering have played major role to transform the manufacturing process of pipes. Manufacturers use technologies like CNC (Computer Numerical Control) machines, robotic welding and automated extrusion systems. As these technologies ensures higher efficiency and better quality of pipes. These technologies are helpful to reduce production time and even minimize human errors.
3.Focus on Sustainability
Due to environmental concerns, manufacturers are adopting eco-friendly practices. They use recycled plastics and metals to produce pipes. Apart from that, energy efficient machines are helpful to lower the carbon footprints. Not only this, but there is also a growing interest in bio-based pipes that are made from renewable materials.
4.Customization with 3D printing
These days, 3D printing technique is gaining more popularity. This technology is famous to create custom-designed pipes and fittings. However, this technology offer rapid prototyping while reducing material waste. Additionally, it offers great flexibility for both manufacturers and customers.
These are some of the emerging trends in pipe manufacturing. These technologies and techniques are predicted to offer innovation, quality and sustainability. As technology is going to be more advanced in coming years, it would create a bright future for pipe industry.